Tability is a cheatcode for goal-driven teams. Set perfect OKRs with AI, stay focused on the work that matters.
What are Warehouse Operations Manager OKRs?
The Objective and Key Results (OKR) framework is a simple goal-setting methodology that was introduced at Intel by Andy Grove in the 70s. It became popular after John Doerr introduced it to Google in the 90s, and it's now used by teams of all sizes to set and track ambitious goals at scale.
Writing good OKRs can be hard, especially if it's your first time doing it. You'll need to center the focus of your plans around outcomes instead of projects.
We understand that setting OKRs can be challenging, so we have prepared a set of examples tailored for Warehouse Operations Manager. Take a peek at the templates below to find inspiration and kickstart your goal-setting process.
If you want to learn more about the framework, you can read our OKR guide online.
The best tools for writing perfect Warehouse Operations Manager OKRs
Here are 2 tools that can help you draft your OKRs in no time.
Tability AI: to generate OKRs based on a prompt
Tability AI allows you to describe your goals in a prompt, and generate a fully editable OKR template in seconds.
- 1. Create a Tability account
- 2. Click on the Generate goals using AI
- 3. Describe your goals in a prompt
- 4. Get your fully editable OKR template
- 5. Publish to start tracking progress and get automated OKR dashboards
Watch the video below to see it in action 👇
Tability Feedback: to improve existing OKRs
You can use Tability's AI feedback to improve your OKRs if you already have existing goals.
- 1. Create your Tability account
- 2. Add your existing OKRs (you can import them from a spreadsheet)
- 3. Click on Generate analysis
- 4. Review the suggestions and decide to accept or dismiss them
- 5. Publish to start tracking progress and get automated OKR dashboards
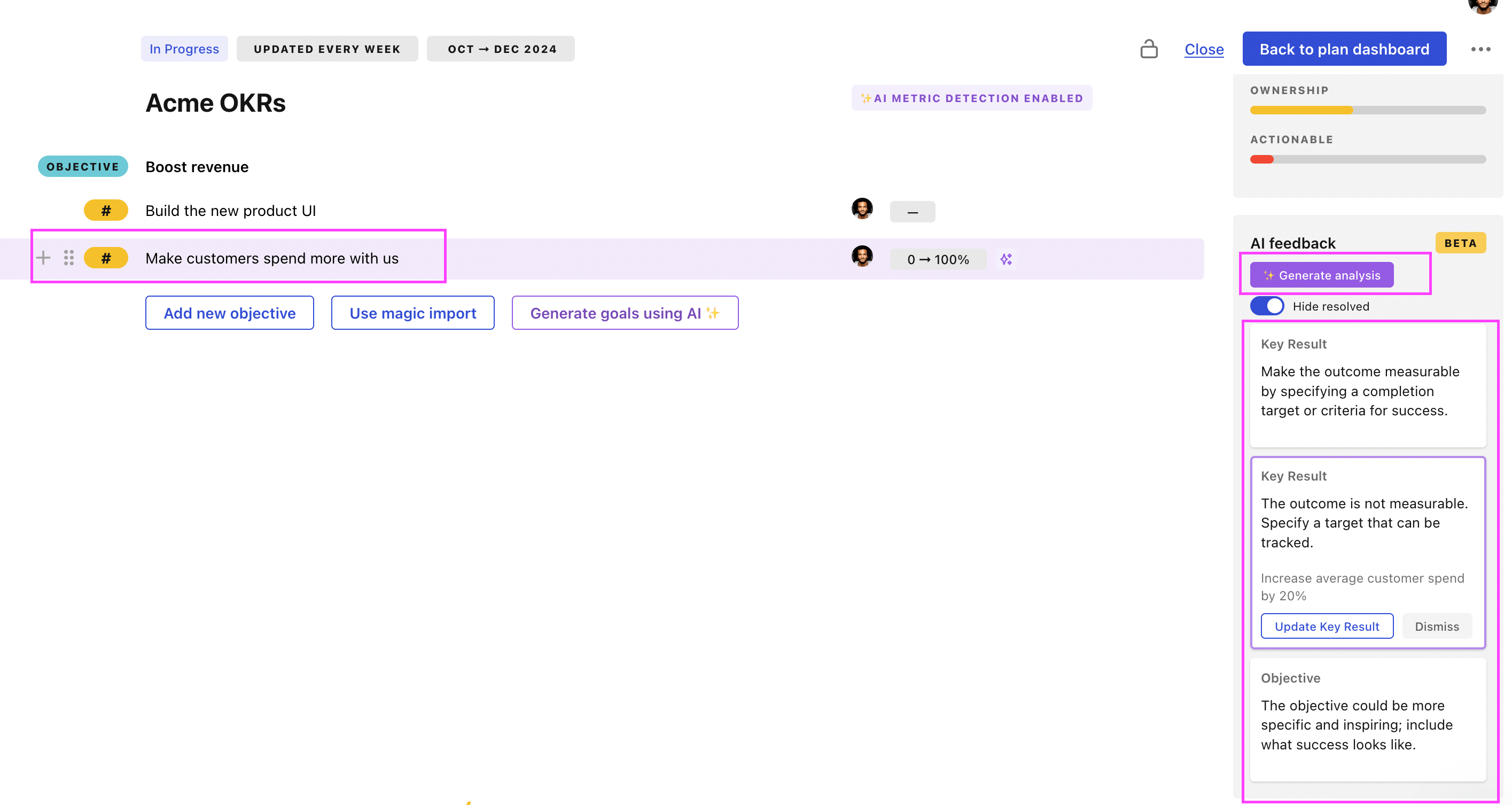
Tability will scan your OKRs and offer different suggestions to improve them. This can range from a small rewrite of a statement to make it clearer to a complete rewrite of the entire OKR.
Warehouse Operations Manager OKRs examples
You will find in the next section many different Warehouse Operations Manager Objectives and Key Results. We've included strategic initiatives in our templates to give you a better idea of the different between the key results (how we measure progress), and the initiatives (what we do to achieve the results).
Hope you'll find this helpful!
OKRs to boost gross margin in warehouse operations
ObjectiveBoost gross margin in warehouse operations
KRImprove warehouse inventory turnover rate by 20%
Implement an efficient automated inventory management system
Conduct regular stock evaluations and adjustments
Train staff on inventory turnover improvement strategies
KRIncrease efficiency of warehouse processes by 15% using lean methodologies
Monitor, assess and improve warehouse processes regularly
Train staff on efficiency-enhancing techniques and procedures
Implement lean methodologies for streamlined warehouse operations
KRImplement a 10% reduction in non-essential operational expenses by quarter-end
Review all non-essential expenses in detail
Develop and enforce a budget reduction plan
Identify areas for potential cost cuts
OKRs to maximize warehouse revenue per square foot
ObjectiveMaximize warehouse revenue per square foot
KRGrow overall warehouse revenue by 30%
Increase sales through targeted marketing strategies
Develop partnerships for revenue sharing opportunities
Improve warehouse efficiency to increase order fulfillment
KREnhance inventory turnover by 15%
Increase marketing efforts to boost product demand
Implement inventory management software for efficiency
Provide staff training on inventory management
KRIncrease warehouse space utilization by 20%
Evaluate current inventory management strategy for inefficiencies
Implement a lean warehouse management system
Optimize warehouse layout using space utilization techniques
OKRs to enhance warehouse inbound efficiency and accuracy
ObjectiveEnhance warehouse inbound efficiency and accuracy
KRReduce inbound processing errors by 40%
Implement regular training sessions for processing teams
Establish a standard protocol for all inbound processing
Upgrade our processing software for better accuracy
KRAchieve at least 95% accuracy in inventory recording
Train personnel in inventory management best practices
Implement a digital system for inventory recording
Conduct regular audits of your current inventory
KRIncrease inbound processing speed by 30%
Streamline existing workflows for higher efficiency
Invest in advanced, faster inbound processing software
Train staff on speed optimization techniques
OKRs to streamline warehouse to delivery process for increased efficiency
ObjectiveStreamline warehouse to delivery process for increased efficiency
KRTrim down transit time by optimizing delivery routes and achieving 15% faster deliveries
Analyze historical delivery data for patterns
Train drivers on efficient driving techniques
Implement GPS tracking for real-time route optimization
KRImplement automation in the packaging process to reduce preparation time by 25%
Train staff on new automation processes
Research suitable automation technologies for packaging process
Purchase and install selected automation equipment
KRReduce errors in order processing and inventory management by 30% using a new software
Monitor error rates and adjust operations accordingly
Identify suitable software to streamline order processing and inventory management
Implement and train staff on software usage
OKRs to enhance warehouse RFP and proforma process efficiency
ObjectiveEnhance warehouse RFP and proforma process efficiency
KRAchieve 90% stakeholder satisfaction through improved communication and transparency in the RFP process
Provide regular progress updates to stakeholders
Train staff on effective and transparent communication skills
Implement a clear timeline for responses in the RFP process
KRIdentify and implement 3 process improvements to increase proforma accuracy
Implement the three most effective improvements
Develop and test potential process improvements
Evaluate current proforma generation process for inefficiencies or inaccuracies
KRReduce RFP preparation time by 25% while maintaining quality
Utilize an RFP software to boost efficiency
Implement a standardized template for consistent RFP formatting
Assign specific roles to streamline the preparation process
OKRs to enhance the efficiency of putaway and picking strategies
ObjectiveEnhance the efficiency of putaway and picking strategies
KRIncrease picking accuracy by 15%
Regularly audit and update inventory management software
Train workers on effective inventory management techniques
Implement barcode scanning system to reduce mispicks
KRImprove order fulfillment speed by 10%
Implement automated inventory tracking system
Train staff in efficient packing techniques
Review and streamline order processing procedures
KRReduce putaway errors by 20%
Monitor and address recurring putaway errors
Train staff on correct putaway procedures
Implement barcode scanning for increased inventory accuracy
OKRs to optimize putaway and picking strategies
ObjectiveOptimize putaway and picking strategies
KRImplement a new putaway and picking strategy into two additional warehouses
Train warehouse staff on new procedures
Monitor and assess strategy effectiveness
Identify necessary changes for new putaway and picking strategy
KRAchieve a 25% reduction in time spent on putaway processes
Train staff on efficient putaway methods
Streamline and optimize putaway process flow
Implement automated inventory management software
KRBoost picking accuracy to 98%
Train staff on best picking practices and techniques
Invest in advanced pick-to-light systems for increased accuracy
Implement regular accuracy audits and error tracking
OKRs to improve product excellence and expedite shipping
ObjectiveImprove product excellence and expedite shipping
KRShorten average shipping time by 20% across all product lines
Optimize warehouse organizational system to improve efficiency
Implement expedited processing for all product lines
Negotiate faster delivery times with shipping providers
KRImplement one new quality control technique and reduce customer complaints by 10%
Research and select a new quality control technique to implement
Train staff in the new quality control method application
Track customer complaints to measure improvements
KRAchieve a 15% decrease in product defects identified through quality checks
Develop new quality control procedures
Implement research on common defect trends
Conduct regular training sessions for staff
Warehouse Operations Manager OKR best practices
Generally speaking, your objectives should be ambitious yet achievable, and your key results should be measurable and time-bound (using the SMART framework can be helpful). It is also recommended to list strategic initiatives under your key results, as it'll help you avoid the common mistake of listing projects in your KRs.
Here are a couple of best practices extracted from our OKR implementation guide 👇
Tip #1: Limit the number of key results
The #1 role of OKRs is to help you and your team focus on what really matters. Business-as-usual activities will still be happening, but you do not need to track your entire roadmap in the OKRs.
We recommend having 3-4 objectives, and 3-4 key results per objective. A platform like Tability can run audits on your data to help you identify the plans that have too many goals.
Tip #2: Commit to weekly OKR check-ins
Don't fall into the set-and-forget trap. It is important to adopt a weekly check-in process to get the full value of your OKRs and make your strategy agile – otherwise this is nothing more than a reporting exercise.
Being able to see trends for your key results will also keep yourself honest.
Tip #3: No more than 2 yellow statuses in a row
Yes, this is another tip for goal-tracking instead of goal-setting (but you'll get plenty of OKR examples above). But, once you have your goals defined, it will be your ability to keep the right sense of urgency that will make the difference.
As a rule of thumb, it's best to avoid having more than 2 yellow/at risk statuses in a row.
Make a call on the 3rd update. You should be either back on track, or off track. This sounds harsh but it's the best way to signal risks early enough to fix things.
Save hours with automated Warehouse Operations Manager OKR dashboards
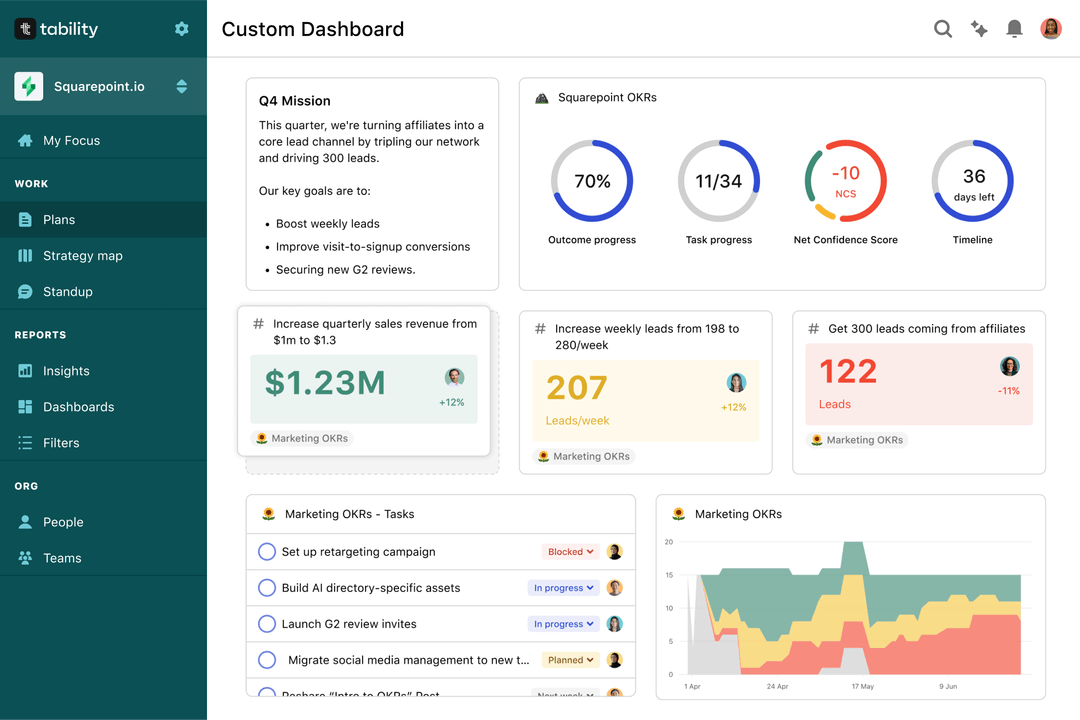
OKRs without regular progress updates are just KPIs. You'll need to update progress on your OKRs every week to get the full benefits from the framework. Reviewing progress periodically has several advantages:
- It brings the goals back to the top of the mind
- It will highlight poorly set OKRs
- It will surface execution risks
- It improves transparency and accountability
Spreadsheets are enough to get started. Then, once you need to scale you can use Tability to save time with automated OKR dashboards, data connectors, and actionable insights.
How to get Tability dashboards:
- 1. Create a Tability account
- 2. Use the importers to add your OKRs (works with any spreadsheet or doc)
- 3. Publish your OKR plan
That's it! Tability will instantly get access to 10+ dashboards to monitor progress, visualise trends, and identify risks early.
More Warehouse Operations Manager OKR templates
We have more templates to help you draft your team goals and OKRs.
OKRs to enhance system stability to improve overall mobility
OKRs to increase cost management efficiency for people and operations
OKRs to boost the overall sales in the upcoming quarter
OKRs to develop a comprehensive new customer database
OKRs to boost overall employee satisfaction and reduce turnover
OKRs to boost product recognition and generate influencer-sourced revenue